Showcases
Vertical Mills
Providing services in all the brands of vertical mills allows for countless cases of success.
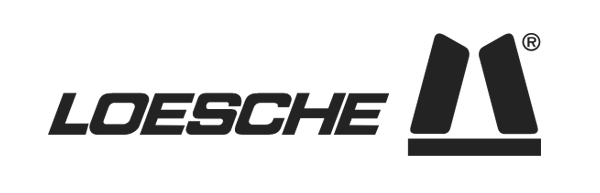
LOESCHE
Latinoamericana S.A.U.
ā⦠The purpose of this letter is to introduce the company IBERMAROS, that is active in the business of cement industry and is a worldwide leader for hardfacing grinding components of vertical mills, on site or in the workshop, since 1993. IBERMAROS have demonstrated references in hardfacing jobs, in the LOESCHE vertical roller mills, that have been executed at the entired satisfaction of their customers. We enclose here the list of the hardfacing jobs made over LOESCHE mills in Spain…”
NEW
SLAG MILL
LM 46 2+2
10 INITIAL
Hardfacing Works
Contracted
By OEM
Warranty
OEM
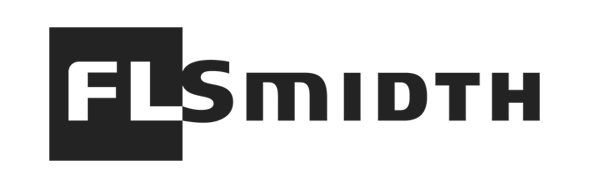
FLSMIDTH ATOX
FLSMiDTH A/S GLOBAL CEMENT TECHNOLOGY, GRiNDiNG TECHNOLOGY
“…For the process of “Hardfacing”, we are pleased to introduce the company IBERMILL, who is active within our industry. IBERMILL is a worldwide recognized service company for hardfacing of the vertical mills grinding components, since 1993 – both at site and in their workshop facilities. IBERMILL technology and welding consumables have been used in successful collaboration with FLSMIDTH, at the satisfaction of our customers. Therefore we are pleased to inform that IBERMILL is now approved and recommended by FLSMIDTH, as hardfacing service provider for the grinding components of ATOXā¢, OK vertical mills as well as rollers for Hydraulic Roller Press⦔
15 Days
intervention
Atox 55 mill
285 km
Welded wire
5 wires
at the same time
Warranty
OEM
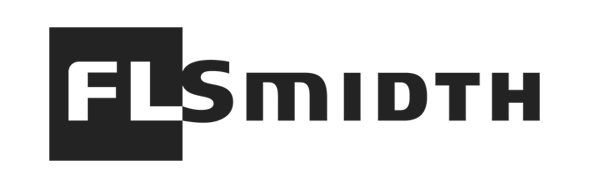
FLSMiDTH OK
Maintain original profiles is of utmost importance to have cement mills operating with highest performance, therefore hardfacing regularly with high wear resistance flux cored wires (IBER 450) is the most flexible and adequate solution for this type of mills. Reverse roller segments could be only a temporary solution.
Ok 39.4
Cement mill
contracted
by oem
Before and after: Picture shows hi-chrome roller segments that have been used and rotated. The yellow wear measure template clearly shows the difference of wear on the roller before and after the in-situ hardfacing has been carried out by IBERMILL. The shape and final result will be very accurate, and the profile is as close to the original profile as possible regardless of whether itās an OK, ATOX or FRM Mill. Typically, the wear rate decreases by 50% (compared to wear rate of Hi-Chrome), meaning that the life time (running hours) of the roller normally doubles.
Warranty
OEM
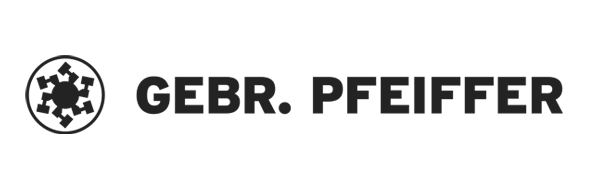
PFEIFFER MILLS
ON SiTE
In case of spare parts availability, hardfacing the roller tires in the workshop and the grinding table in-situ, could be a very interesting solution.
MPS 3350 B
Rawmill
2 days
TABLE HARDFACING
MPS 4000 B
Rawmill
Wear rate
before hf
1,3 g/ton
6 months After hf
0,7 g/ton
MPS 4120
Raw mill
Dam ring
Hardfaced
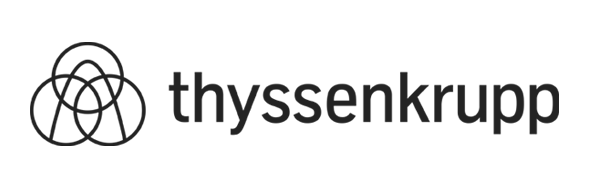
KRUPP POLYSIUS MILLS
ON SiTE
No matter the age of the vertical mill, hardfacing with IBERMILL the grinding components on a regular basis enable great achivements.
Partnership
Since 1996
54 / 27
Raw Mill
46 / 23 Raw Mill
20 years
Without using spare parts
51 / 26 Raw Mill
Spare parts
Hardfacing in workshop
10 tons roller tire
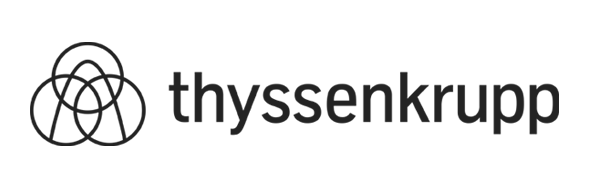
KRUPP POLYSIUS MILLS
ON SiTE
No matter the age of the vertical mill, hardfacing with IBERMILL the grinding components on a regular basis enable great achivements.
Partnership
Since 1996
46 / 23 Raw Mill
20 years
Without using spare parts
54 / 27
Raw Mill
51 / 26 Raw Mill
Spare parts
Hardfacing in workshop
10 tons roller tire
ROLLER PRESS
ON SITE AND WORKSHOP
Hydraulic Roller Press units have been developed for material grinding, anyhow, most of the cement plants use HRP unit before ball mill for pre-grinding, saving energy and increasing capacity. Roller shafts are made of solid forged body or with shrink fit sleeve, provided with a renewable multiple layer of deposit welding. Surfaces must be rewelded when the wear protection layer worn out.
HRP
For Clinker
Remove
Hard Overlay
BY GOUGING